Gilgen Logistics’s New PERFORMANCE Stacker Crane
Faster, More Compact and More Economical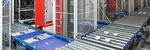
Stacker Crane
Stacker cranes are the key component of high-bay facilities and therefore crucial to the efficiency and cost-effectiveness of any logistics solution. At LogiMat, the industry’s most important trade fair, Gilgen Logistics will be presenting its new generation of stacker cranes for high-bay storage facilities. These units are tailored to customer needs in terms of space utilization, throughput, safety, operation, sustainability and cost-effectiveness.
Maximum acceleration and best use of space
“The significantly higher level of performance provided by our equipment means that in many cases we can rely on single-mast units with one load-handling device, whereas our competitors install a much heavier double-mast version with two load-handling devices. We therefore require less steel for the same performance, resulting in a positive impact for customers in terms of price,” Thomas Riffert, head of stacker crane development at Gilgen Logistics, added.
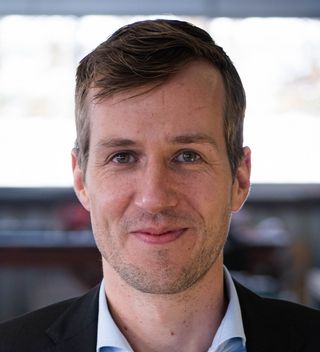
Our teams’ wealth of experience and development expertise goes into these devices. We are very proud of this innovation,
Daniel Gilgen, CEO
Maximum acceleration and best use of space
A form-fitting travel drive at the top and bottom significantly reduces mast vibrations, prevents the drive wheels from slipping, and enables maximum acceleration and speed rates. This latest generation thus boasts twice the acceleration rate of its predecessor. On top of that, Performance units also offer much more than just high throughput. Advantageous stop clearances, a slim mast design and the absence of hydraulic buffers all go to increase storage capacity. Michael Hediger, head of the Systems division, commented about this, saying: “We offer our customers optimum use of space owing to a compact design. This technology allows us to build mini-load stacker cranes up to a height of 25 meters and pallet stacker cranes up to a height of 45 meters – convincing advantages compared to other solutions on the market.”
Facts
Paletts | Container | |
---|---|---|
Speed of running gear: | 5 m/s | 5 m/s |
Acceleration rates of running gear: | 0.5 - 2,5 m/s² | 2-3 m/s² |
Speed of hoist: | 1 – 1.5 m/s | 3 m/s |
Acceleration rates of hoist: | 1 – 1.5 m/s² | 3 m/s² |
Design heights: | 5 – 45 m | 5 – 25 m |
Other advanteages
- Weight reduction: up to 25 %
- Increased performance: up to 20 %
- Smaller stop clearances: up to 25 %
- Innovative load-handling device: more space-saving and faster
(Image: A 30 m high Gilgen stacker crane Perfomance for pallets.)