Digitalisation
Digitalisation Meets Automation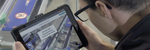
Augmented Reality
Walk Virtually Through the Facility and Assist in MaintenanceDigitised Down to Every Single Screw
For several years, we have started exploring and developing the possibilities of digitalisation on intralogistics systems.Augmented Reality makes digitalisation visible and can support work in various ways
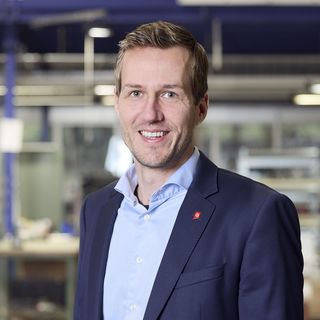
We aim for our systems to be an important part of our customers' value chain as part of Industry 4.0. Thus, all our conveying systems will be digitally supported in the future and push automation further
Daniel Gilgen, CEO
Digital Facility
With the Digital Facility, the customer can directly access all information such as plans, service dates, various statistics, and spare part numbers without searching through long lists. Along with animated instructions, the safety in handling the facility is increased and errors are reduced. This is a Just-in-time know-how transfer. At the same time, the process at Gilgen Logistics is accelerated and simplified. Where previously hundreds of paper pages were used for parts lists in assembly production, now almost only digital work is done.
Advantages and Benefits
With the digitalisation of the intralogistics facility, sustainability, efficiency, operability, and availability are all enhanced.- The communication between the facility operator and the manufacturer is simplified due to the available information and its simplified retrievability via the QR code.
- Through remote support, a specialist can intervene on the facility. This leads to shorter reaction and also downtime. Additionally, this saves travel costs.
- A significant amount of paper is saved over the lifetime of the facility.
- The most important information about the facility is directly and clearly available.
- Manufacturers and customers save time throughout the entire process, and errors are minimized.
- Maintenance operations by the manufacturer are transparently reported and can be accessed at any time.
- A spare parts order can be automated.
- Animated maintenance and assembly sequences simplify the work and create trust.